FLEXIBLE PRINTED CIRCUITS
FPC and FFC design and manufacturing
Flexible Printed Circuits
KEYFLEX offers a comprehensive range of flexible printed circuit (FPC) services, including tooling and part supply, to suit clients’ needs. Our FPCs are made of polyimide or polyester film, which makes them highly reliable and excellent flexible printed circuit boards. They have the characteristics of high wiring density, lightweight, thin thickness, and good bendability. FPCs are unique because, unlike PCBs, they can bend and flex. Furthermore, they typically offer greater heat dissipation than their PCB counterparts, which can prolong the electronics in which they are used.
All FPCs are made using a flexible substrate, such as polyimide. FPCs can be further categorized as rigid-flex or flat flexible. Rigid-flex circuits are a combination of rigid and flexible circuits that are interconnected by plated through holes. Flat flexible circuits are made of a single layer of conductive material that is laminated between two layers of insulating material.
Our FPCs are designed to be lightweight, thin, and flexible, making them ideal for use in appliances where a circuit that can be moved frequently is required, such as on a hinged lid. As the copper is bonded to the polyimide, the flexible circuit can withstand flexing and movement without any adverse effects. Components such as LEDs and switches can be soldered to the circuits, and locally applied stiffeners allow bulkier components such as IDC connectors to be applied.
Our FPCs can be cut to any shape or size, meaning a circuit can incorporate multiple flexible tails, removing the need for extra ribbon cables between PCBs. With the copper being chemically etched to form the track-work, an intricate and complex multi-layer flexible circuit can be created that can be finished in a variety of processes such as gold plating.
Our team of experts is dedicated to providing you with the highest quality products and services. Contact us today to learn more about how we can help you with your next project.
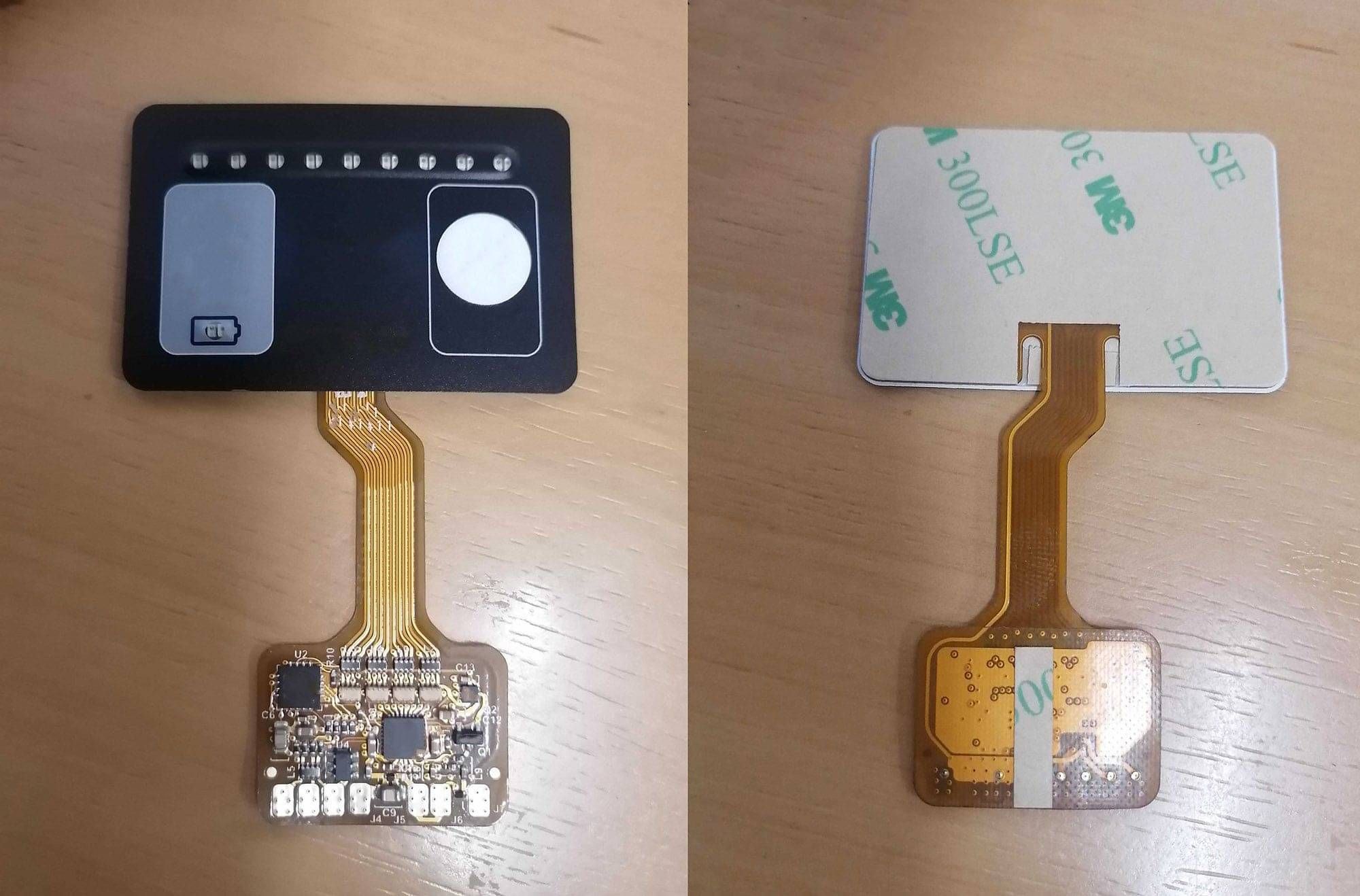
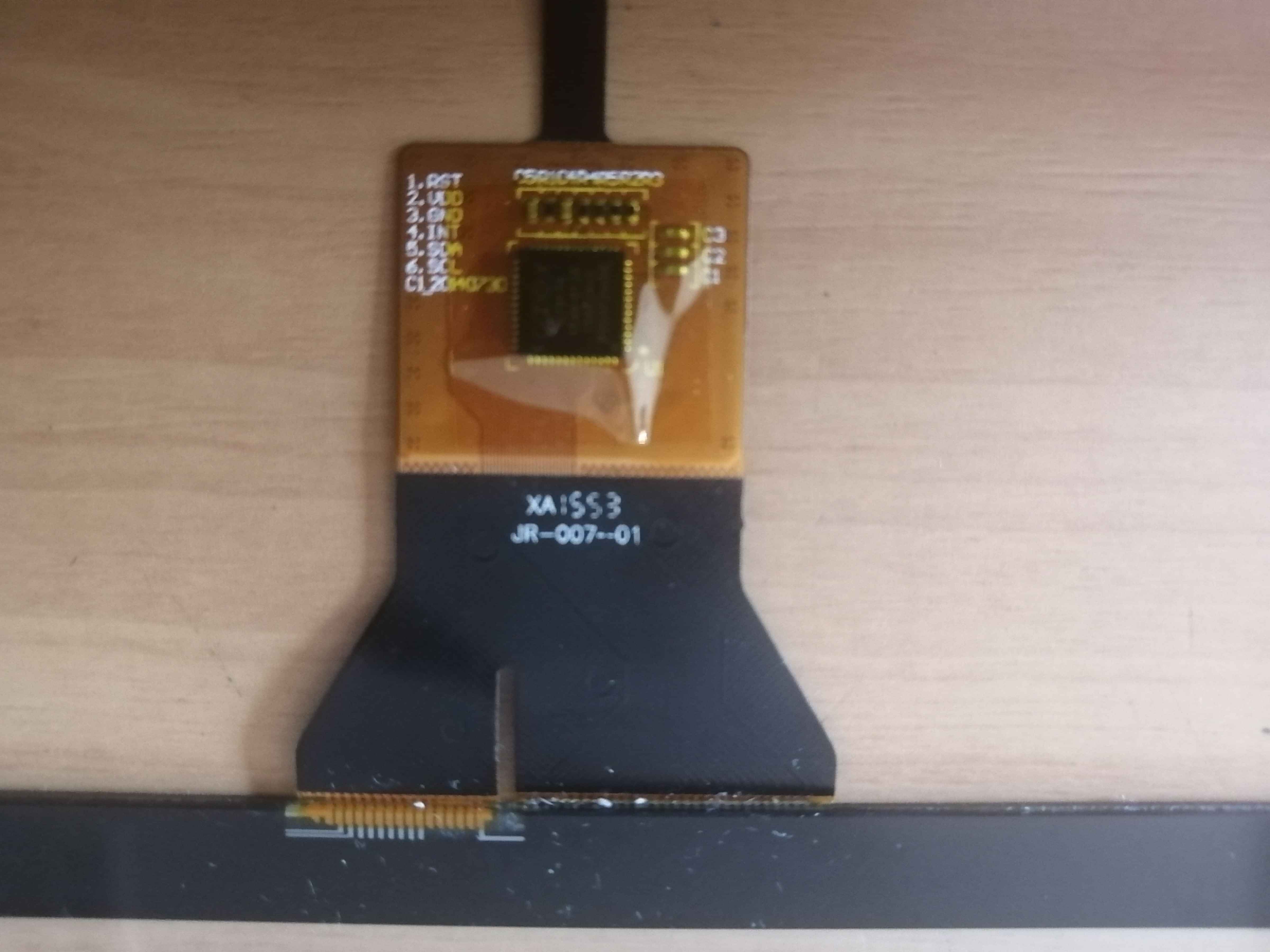
Advantages of Flexible Circuit Design
Reduce messy, time consuming wire harnesses
Space and weight reduction coupled to robust connections and fast assembly
Excellent performance in high vibration applications- flexibility reduces stress on solder joints
Polyamide covering protects circuits in harsh environments
Excellent performance in high speed signal transmission applications
Uniform spacings between conductors and ground helps to control impedance and reduce crosstalk
Common questions regarding Flexible Circuit design?
"What is the minimum bend radius that I can work with?"
A good rule of thumb to go by is a minimum of 6x the circuit thickness with single layer flex circuit the best choice for flexible areas. Typically, a layer is 0.15mm thick
Single-layer: 6 × circuit thickness (minimum)
Double-layer: 12 × circuit thickness (minimum)
Multilayer: 24 × circuit thickness (minimum)